コニカミノルタのコア事業の一つであるオフィス向け複合機。そのバリューチェーンは半導体不足とコロナ禍による物流の混乱で一時的に大きな影響を受けた。しかし、関連する部門間の緊密な連携と迅速な意志決定、現場力の発揮によって、一時は膨らんだ受注残も2022年度第3四半期には大幅に改善、危機を脱しつつある。後編では、高水準の仕様と品質を維持しながら調達可能な半導体に合わせて設計を変更するという逆転の発想で製品を送り出し、部品サプライヤーとの関係強化も実現した開発現場の対応について、上席執行役員 情報機器開発本部本部長の廣田好彦に聞いた。
複合機は多様な技術集積の結晶
業種や企業規模にかかわらず、あらゆるオフィスに欠かせないデジタル機器―それがオフィス向け複合機だ。MFP(Multifunction Peripheral:多機能周辺機器)とも呼ばれ、その名の通り、コンパクトな筐体でありながら、プリント、コピー、スキャン、FAXなど、多彩な機能で業務プロセスを支援する(図1)。単に多用途というだけでなく、顧客の使い方に合わせてコンフィグレーション(オプション構成や初期設定)をカスタマイズした上で届けられる「お客様先へ設置するまでに価値を積み上げていく」ソリューションである。
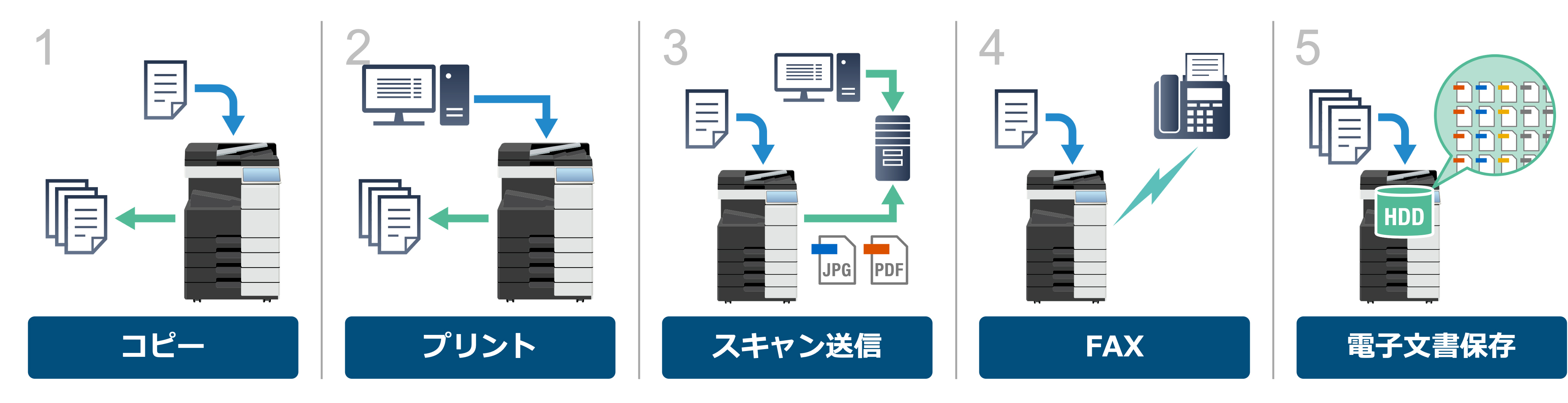
図1 複合機には5種類の基本アプリケーションが存在する
こうした機能を実現するため、高精細に文書や写真などを撮像・処理するための光学技術、画像から得た光信号をデジタル処理する電気・電子技術、紙送りや転写などを行うためのモーターなどの機構技術(メカトロニクス)、プリント出力をしながら書類をスキャンして電子化するといった複数の動作を同時に高速制御するためのソフトウエアやコントローラー技術など、多種多様な技術が集積している(図2)。消耗品として提供されるトナーには高度な化学プロセス技術が用いられている。
「よく『電子化の進んだ自動車は多様な技術の塊だ』と言われますが、複合機も同様にさまざまな技術の結晶なのです」と廣田は強調する。こうした多様な技術が集積している複合機にとって、半導体供給が止まるという事態がどれだけ影響を及ぼすかは想像に難くない。
個別の半導体をコニカミノルタが調達するという状況は実はそれほど多くない。紙送りなど可動部分を制御するモーター制御ユニット、光学センサーで読み取った画像信号をデジタル化する光学センサーユニットといった、ユニット単位で調達する割合の方が多いのだ。ところが、そういったユニットのサプライヤーも必要な半導体の確保ができなくなり、コニカミノルタへのユニットの供給が滞ってしまった。
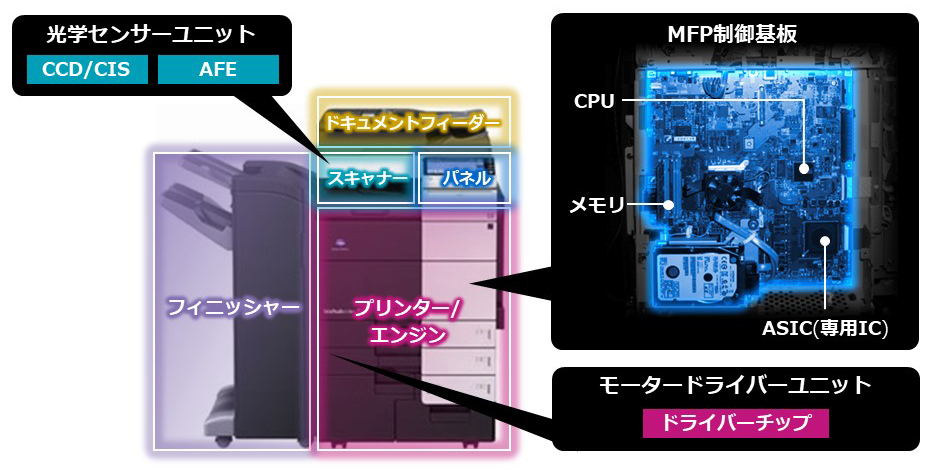
図2 複合機は多様で複雑な機能を制御するため、小型高性能の半導体を数多く搭載している
前編で紹介したように、生産・調達本部、開発本部、SCM部などが緊密に連携し、ユニットサプライヤーへの聞き取りにより不足している半導体を特定、半導体メーカーと直接交渉し、使用可能な半導体の供給を依頼した。しかし、全く同一の半導体を調達することは困難な情勢であり、廣田をトップとする開発本部は、経験したことのない逆転の発想で難局に挑むこととなった。
入手可能な半導体に合わせて設計を修正する日々だった
半導体不足という困難は、光学センサーユニットの供給停止で始まった。「ローエンドの複合機で用いられているCIS(Contact Image Sensor)というユニットが入らなくなりました。イメージセンサーの信号を調整してデジタル変換するアナログ・フロントエンド回路(AFE)というチップの供給が止まったことが原因です」(廣田)
「そこで、『ユニットの中の基板を我々が設計するから、それを組み込んで納入してほしい』とサプライヤーに依頼したのです。このようなことは未だかつてやったことがありませんでした。光学センサーユニット内の基板変更の影響で、複合機内の他の部分も設計変更することになりましたが、最初の難局を乗り越えることができました」。
しかしその後、世界中でありとあらゆる半導体供給が停滞した。廣田は、「毎週のようにあれがない、これが足りないとアラートがでる状態でした」と当時を振り返る。
「紙送りなど可動部分の心臓部であるモーターを制御するドライバーチップの欠品には苦労しました」と廣田。これは低価格であることを理由にX社のみを調達元としていたもの。別のY社も類似のドライバーチップを販売していたが、その頃には世界的に半導体の取り合いになっていて調達できなかったという。そこで廣田らはX社に対し、「基板を設計し直すので、御社が提供可能なチップを供給してほしい」と要請。同時に価格が高いからと購買を控えてきたY社に対しても、今後の採用を条件に供給を依頼した。
「自分たちの要求仕様に合わせたチップを選ぶのではなく、入手可能なチップで同じ機能・性能を実現する――そういう逆転の発想に変えたのです。1種類の別チップだけでは複合機の全ラインアップをカバーする量を確保できなかったので、モーター制御ユニットでは最終的に製品ごとに7種類もの基板を設計しました」と廣田は言う。
複合機全体のメカニカル制御やオプション制御では、車載業界でよく使用されるZ社製CPUを多数使用していた。この代替品として「ARMコア」というプロセッサーを検討したが、これもまた供給不足が懸念された。さらにARMコアは英ARM社の設計思想に準じた複数の供給元があるが、完全な互換性はなく、チップをただ交換するだけで動作するわけではない。そこで開発本部では、Z社製チップや複数のARMコアCPUのいずれでも動作するように設計変更し、駆動ソフトの立ち上げ時に判別して切り替えられるようにした。
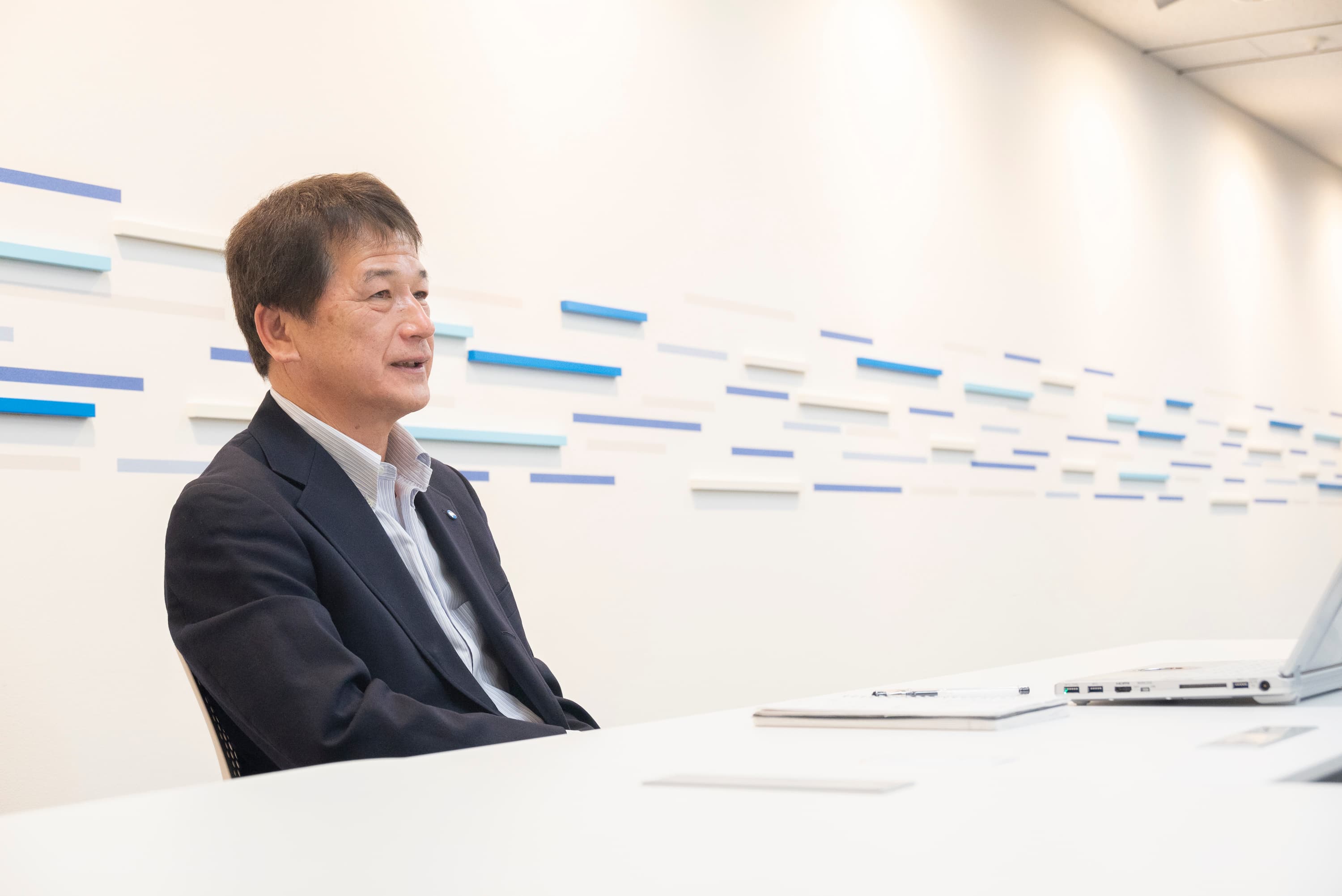
「半導体供給の停滞で毎日のようにアラートが出る状態でした」と廣田好彦・上席執行役員 情報機器開発本部本部長
現場に権限委譲して即断即決で問題に対処
「発想の転換」と口で言うのは簡単だが、目標とする機能・性能を定めて要求仕様を策定し、必要な部品を決定するというプロセスを繰り返してきた開発エンジニアが、使える部品に合わせて再設計するという真逆の課題にどうやって対応できたのか。カギとなったのが情報共有の徹底だった。
「コロナ禍になって以来、開発本部では、部品供給に関する生産・調達本部からの情報や設計変更の進捗状況を共有するため、毎週1回、対策会議を開いてきました。関係者が集まって現場の担当を決め、その担当者が上がってくる情報を基に即断即決する―という基本方針で臨みました」(廣田)。
現場担当者に権限を委譲し、即断即決で動くモデルは、前編で紹介した生産・調達部門やSCM部門の対処と共通するものだ。これがコニカミノルタのものづくりの〝現場力〟として、強靱なレジリエンスを発揮したと言える。
製造プロセスのコスト削減と他事業部のビジネスにも開発部門が貢献
一方、半導体不足でやむを得ないとはいえ、頻繁な設計変更や調達部品の変更はコスト上昇を引き起こしかねない。しかし廣田は「たしかにインパクトは大きかったのですが、開発、生産・調達部門一体でのコストダウン活動によって、わずかな上昇に留めることができました」と述べる。
例えば、マレーシア工場では、開発本部から2人の要員を出向させている。製造現場を見て不具合が発生している工程を洗い出し、設計段階で問題発生回避に取り組んでいる。「製造ラインで生じるプラスチックから出る不純物が、複合機の現像ユニットに入り込み、不具合発生の原因になっていることを発見しました。そこで、不純物が出ないような加工方法を開発部門が考案し、工程を変更しました。開発と生産が一体となって現場の課題を精査し、改善することで、良品率を上げながらコストダウンを実現しています」(廣田)
こうしたグローバルに広がる現場からの情報を集約して膨大な量を蓄積し、それをデータサイエンスの手法を使って分析、どのパラメータをどう変化させると歩留まりが安定するか―といった解析を行って、工程を改善させる試みも進んでいるという。
さらに、複合機の開発で得た知見をもとにロボティクスでも一歩踏み出している。「複合機開発では光学、電気・電子、メカトロニクス、コントローラーと多岐にわたる技術を必要としますが、蓄積された多様なノウハウのうち、モーターの制御や光学認識などはロボット開発に応用できます。このロボティクス技術は弊社の他の事業部のビジネスにも貢献しています。例えばセンシング事業ではICT端末の外観検査工程で使用する測色機を製造、販売していますが、ある測色機の納入先様から検査工程フロー自動化の依頼をいただき、この技術を応用することで実現しました」(廣田)
このようにして半導体不足という困難をしのぎ、「開発部門としてサプライチェーンを学ぶことの重要性に改めて気づきました」と廣田は話す。さらに、「今回の経験を糧に、特定の一社に過度に依存しないよう調達部門やその先のサプライヤーとの関係強化を図り、データサイエンスやロボットを活用した開発・生産プロセスの見直しなどをさらに進め、レジリエンスを一層高めていきたいと考えています」と危機を乗り越え成長し続ける、これからの開発のあり方を展望していた。
*Imaging Insightのこちらの記事も併せてご覧ください。
関連リンク
暮らしの「光」と「色」を守る計測技術、産業界の成長支えるコア事業の根っこに迫る | KONICA MINOLTA(コニカミノルタ)